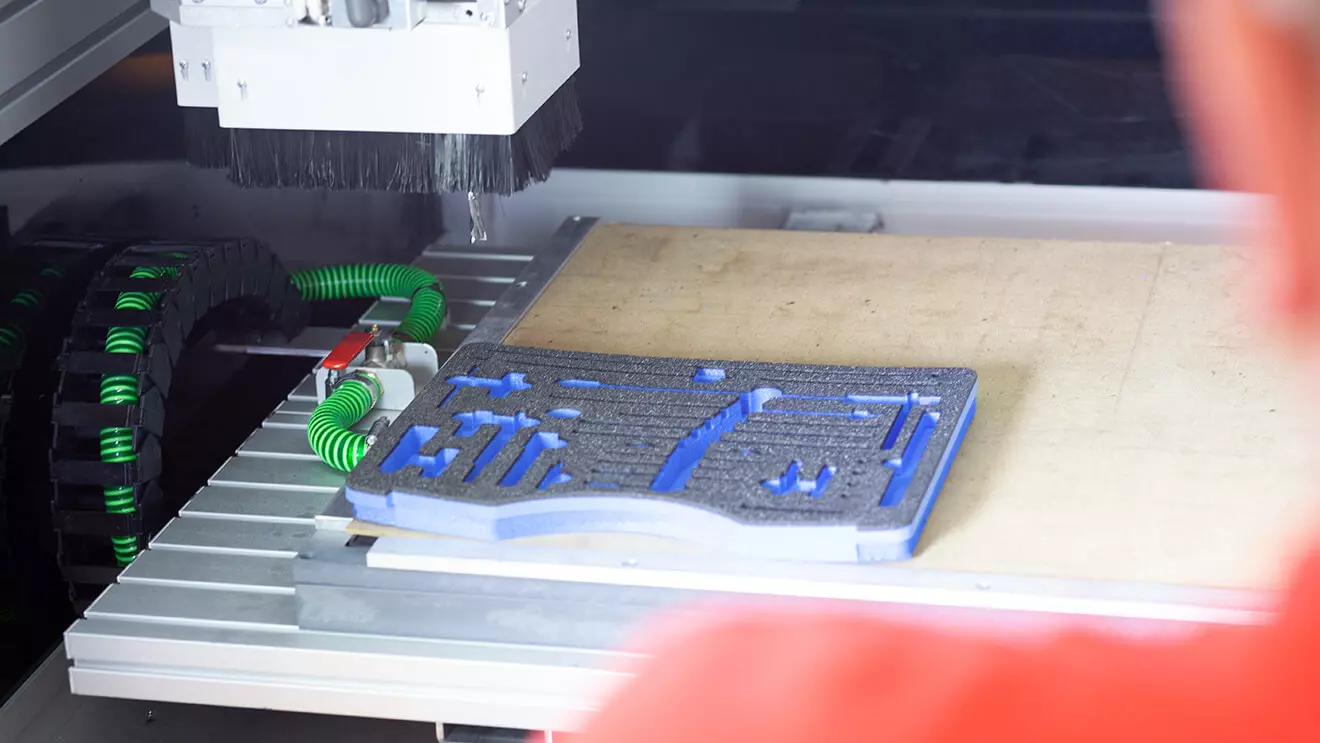
“Popular milled inlays: stable and multicoloured”
Milled inlays are very popular as they are very stable due to the fact that they consist of just one piece of foam.
It is also possible to mill multi-coloured foams, e.g. for subsequent completeness checks of the packaged contents.
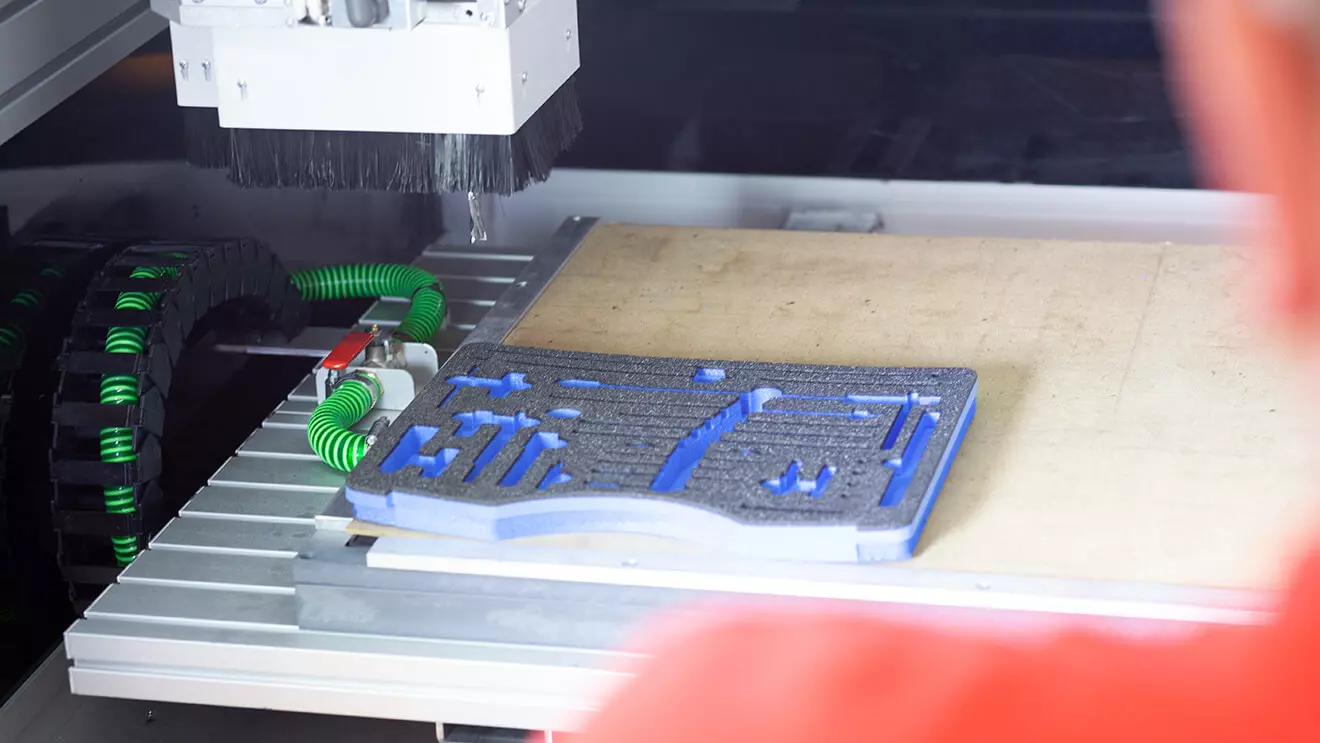
Case printing at W.AG has strong advantages
- Imprinted logos, advertising messages and your own photos create attention and trust in your company and your brand.
- Illustrations of the contents or instructions for use on the outer shell increase functionality.
- High-quality and durable printing with screen or pad printing, digital printing or IML, the top class among printing processes.
- Optional integration of Digimarc with IML printing for convenient retrieval of information via app.
- Customised design of the case fasteners with logo imprint or logo embossing.
- Complete handling of the pre-press stage by W.AG.
- Detailed advice from our experienced consultants by telephone and on site.
- Top service including the production of sample cases.
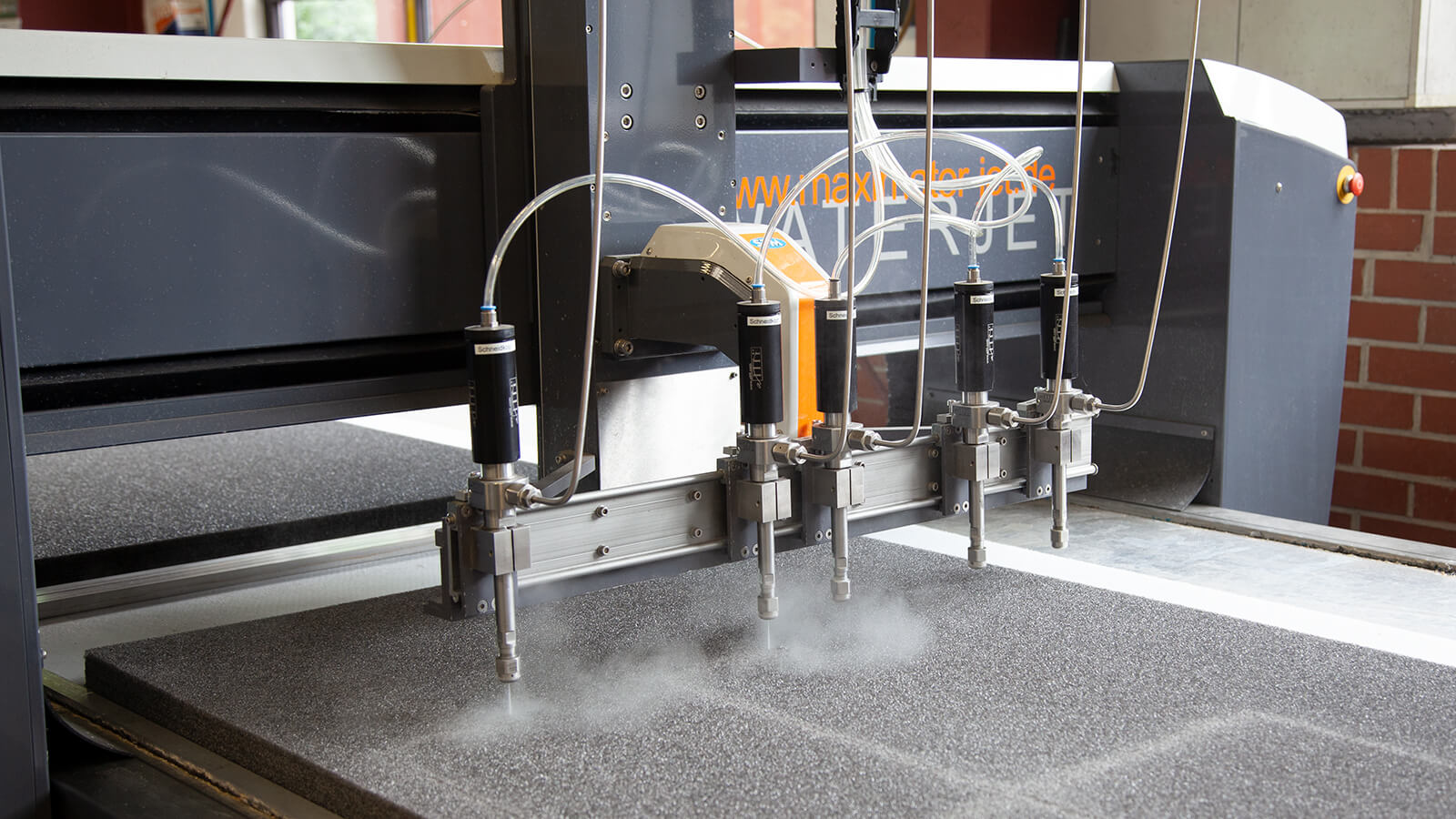
Modern processes
During water jetting, attention is paid to optimum material utilisation thanks to the auto-nesting function, which ensures maximum utilisation of the foam sheets for large quantities. Quick adjustments and changes can be made directly on the waterjet machine. Our employees monitor the waterjet cut and thus guarantee the highest quality. The individual layers of the water jet cuts are then dried and glued into individual inserts by our employees at our gluing stations.
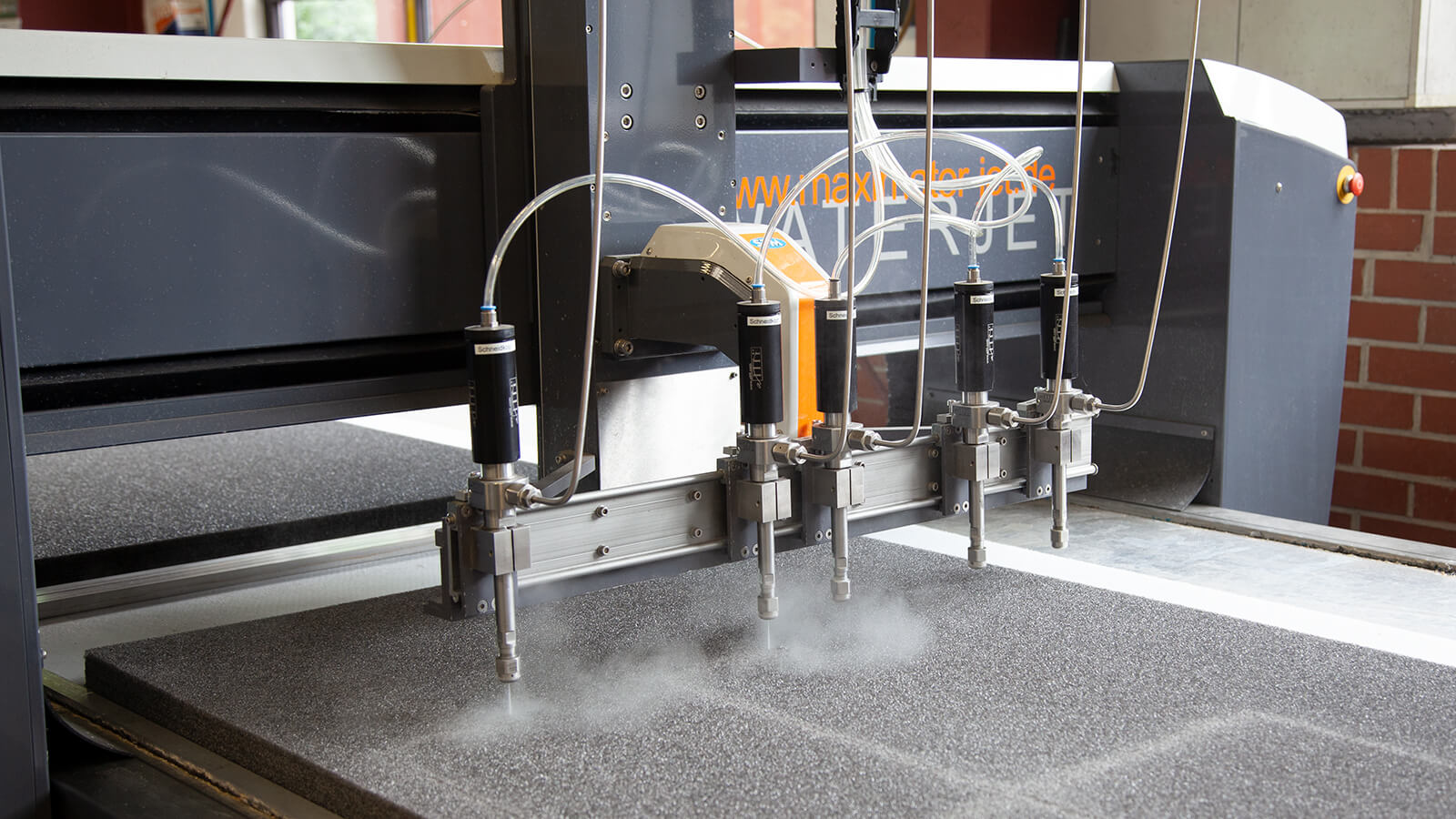
Laser cutting
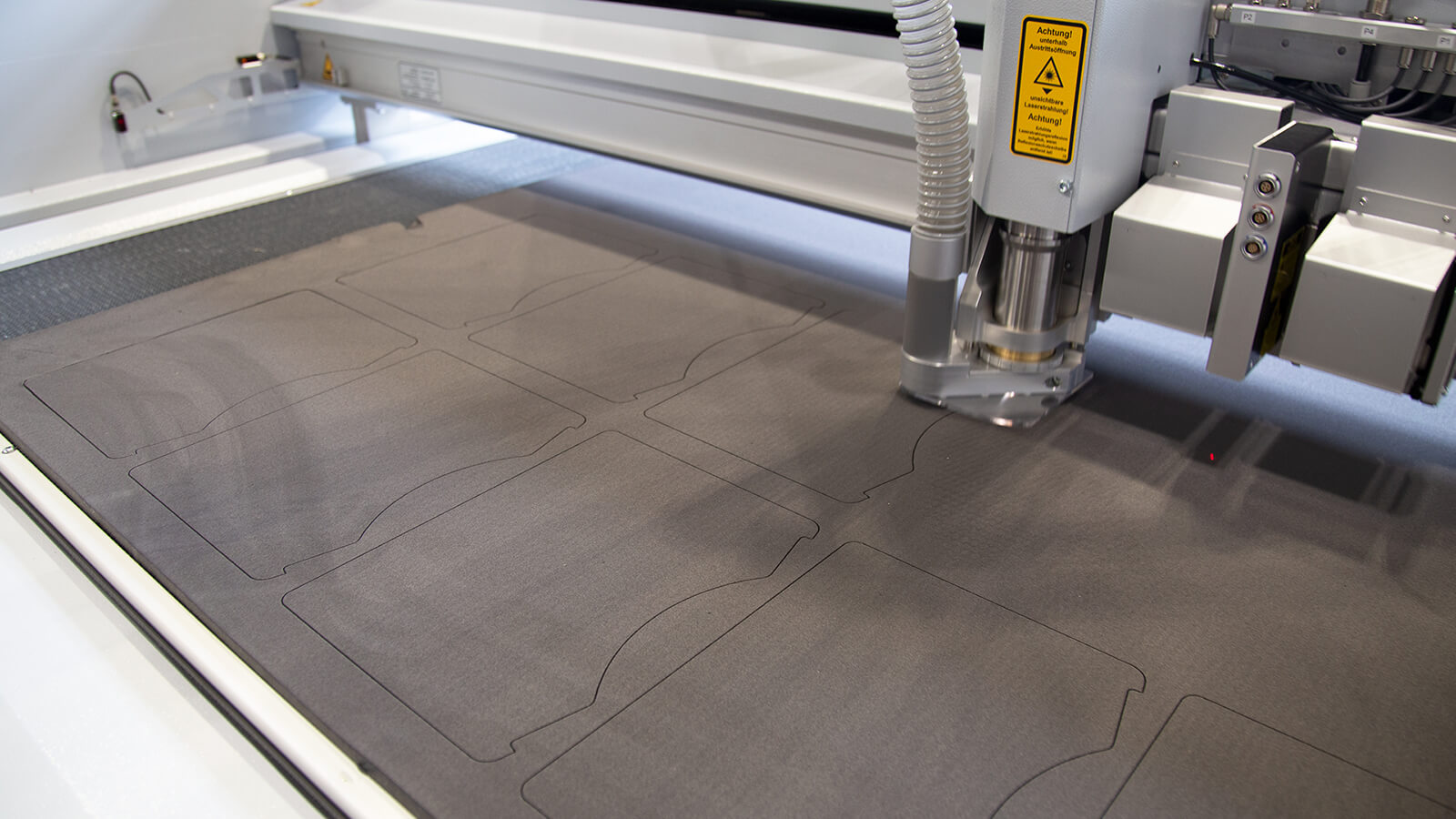
Laser cutting is a new processing technique in W.AG foam processing. Similar to water jetting, a laser cuts the foam according to a specified drawing and makes it possible to produce individual foam layers. Further processing for foam inlays is carried out in a similar way to water jetting. However, laser cutting offers the advantage that the cut foam does not need to be dried. This enables faster production of the individual foam components.
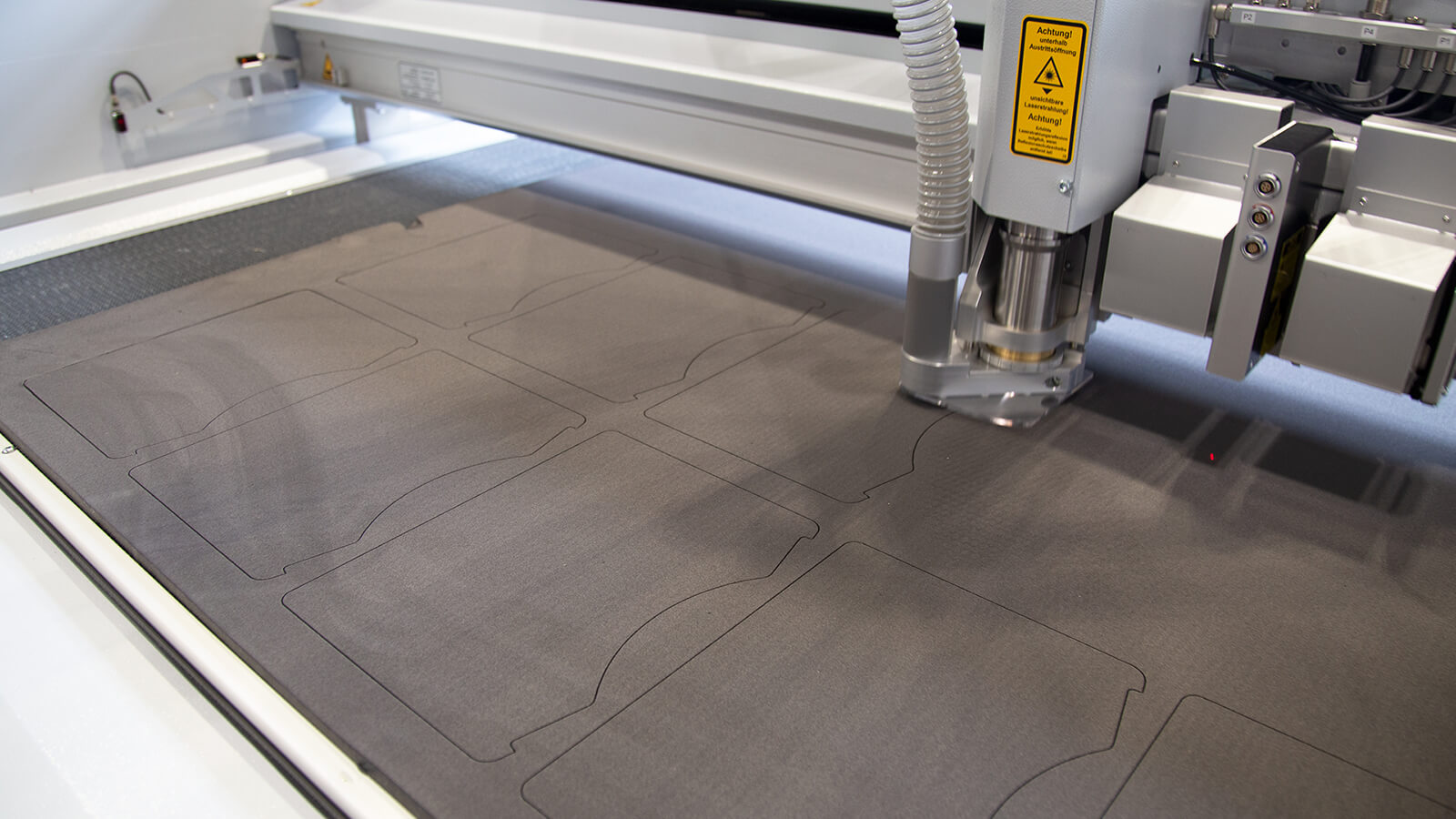
Laser engravings
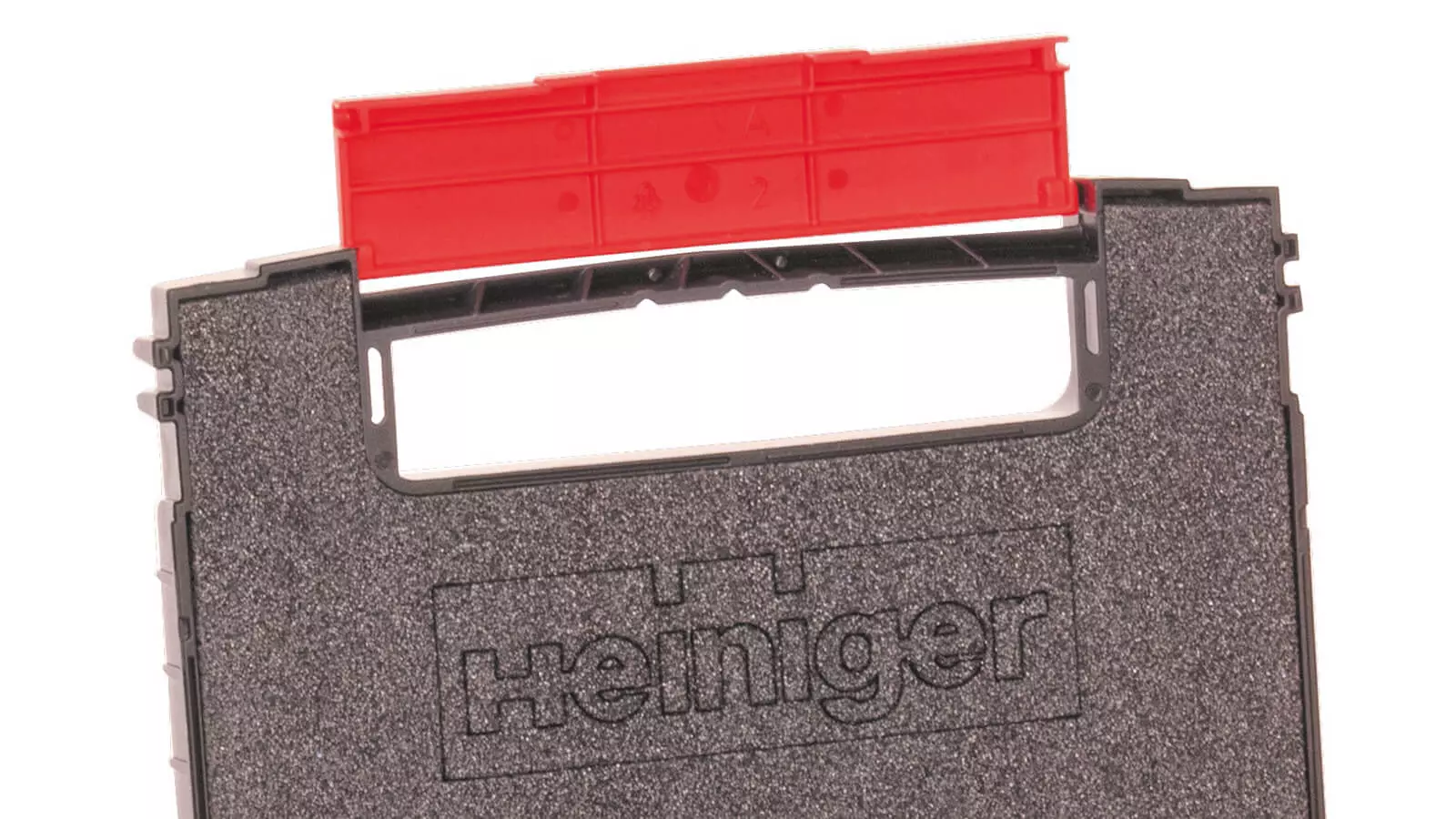
W.AG offers high-quality laser engraving as a decoration option for inlays. Logos and product information can be displayed directly on the inlay for a professional presentation. For example, your brand logo can be communicated on the inlay or labelling can be used to create real added value for the customer.
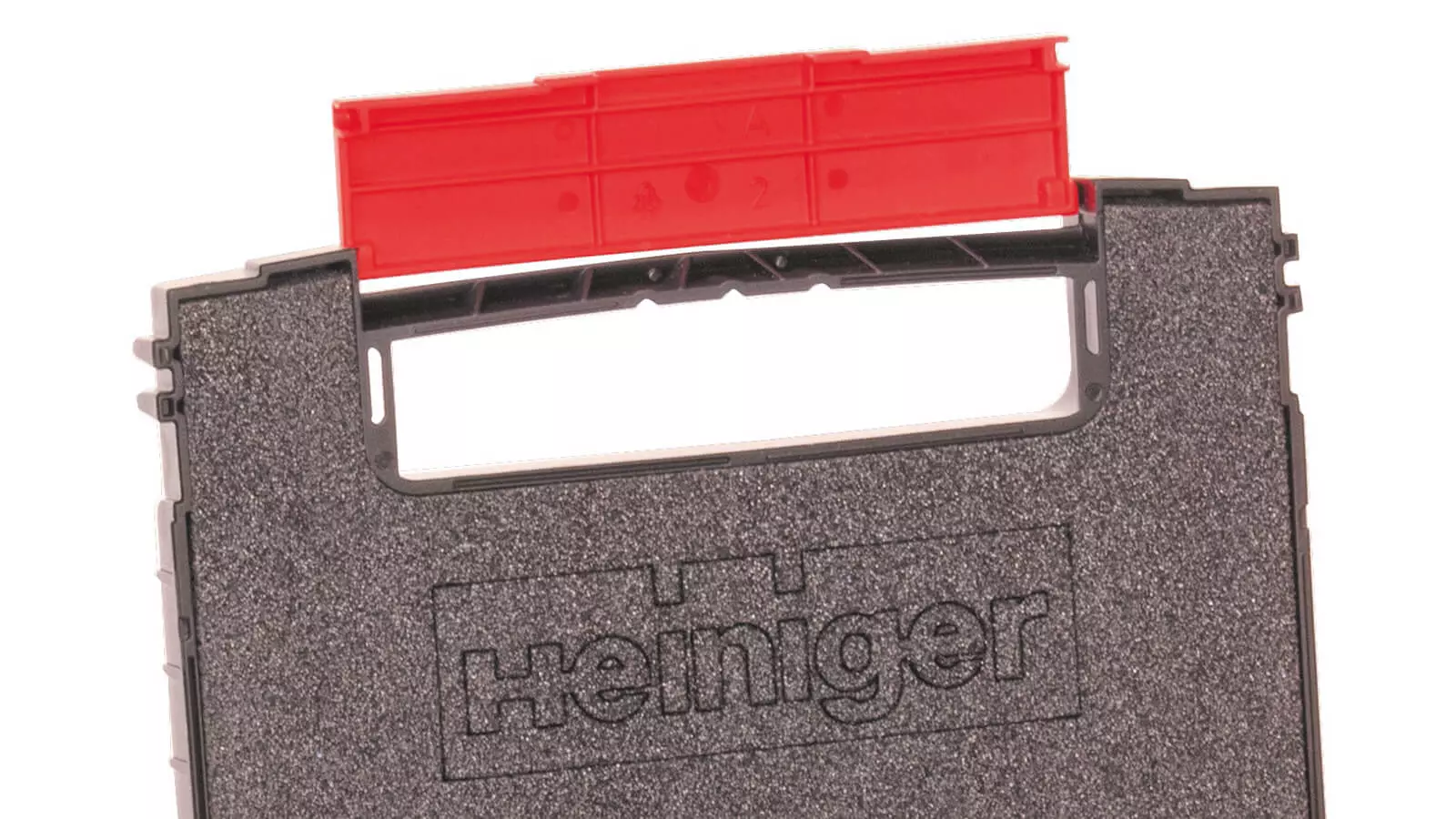
Punching
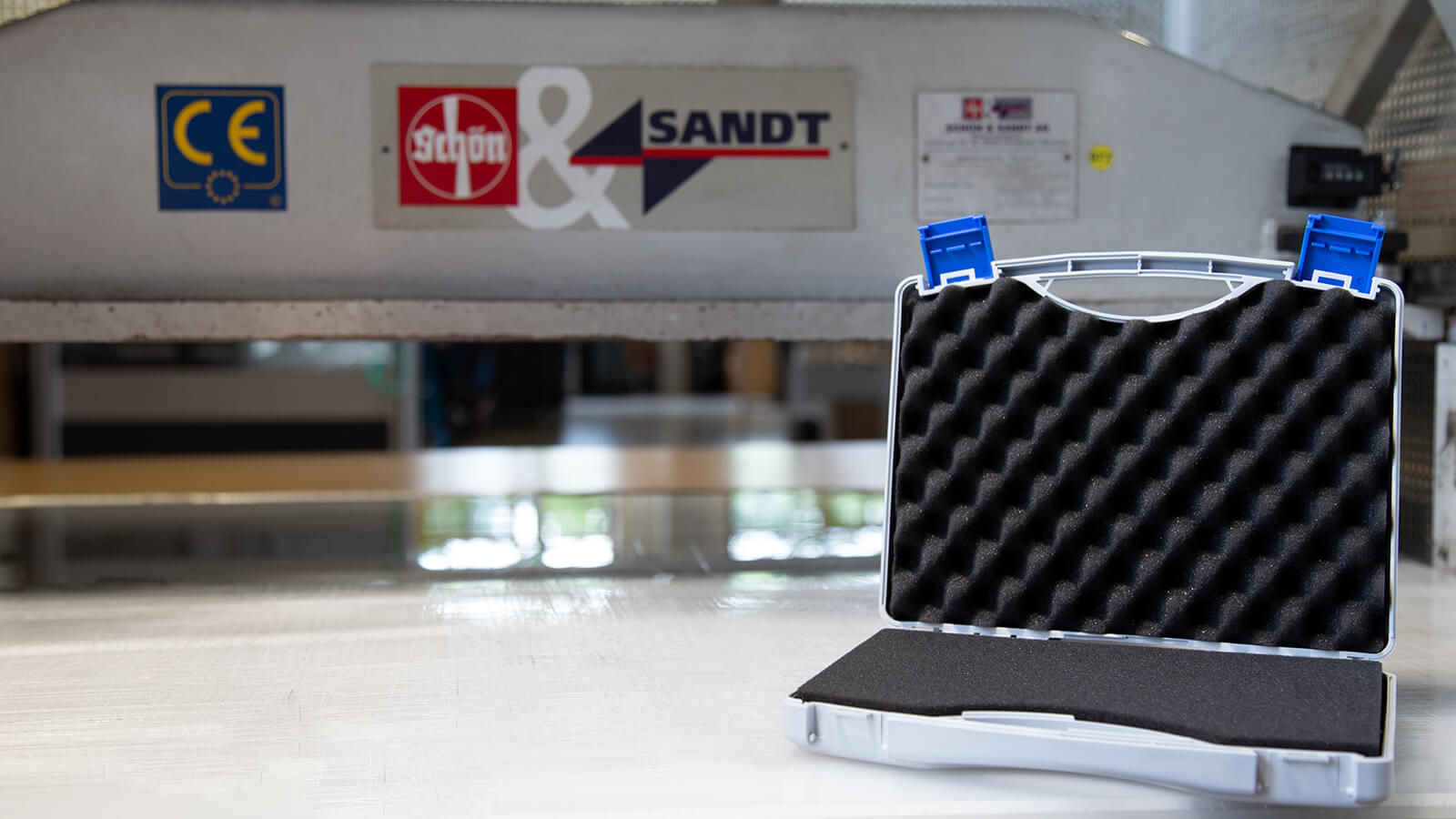
The punching of hard and soft foams is the simplest way to produce case inserts for a suitcase. W.AG uses the punching technique in which suitcase contours are punched out of foam sheets using punching knives, e.g. to produce dimpled foams for the upper shells of suitcases.
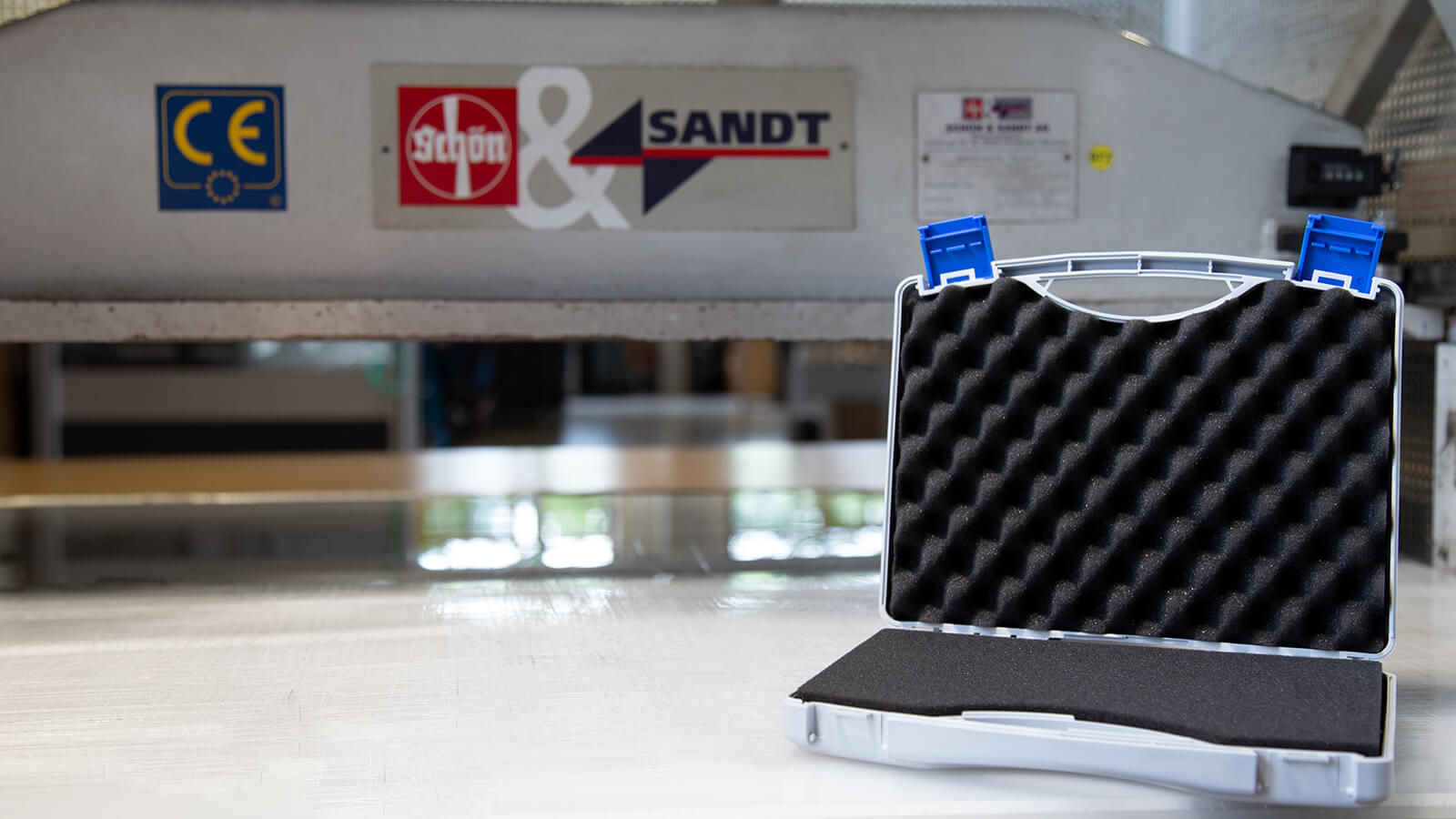
This is what we stand for
Ready for innovation?
Contact us